Considerations when buying plastic-extrusion or injection-molding equipment
- Wayne Conrad
- Apr 15, 2019
- 4 min read
The lowest price is not necessarily the lowest cost!
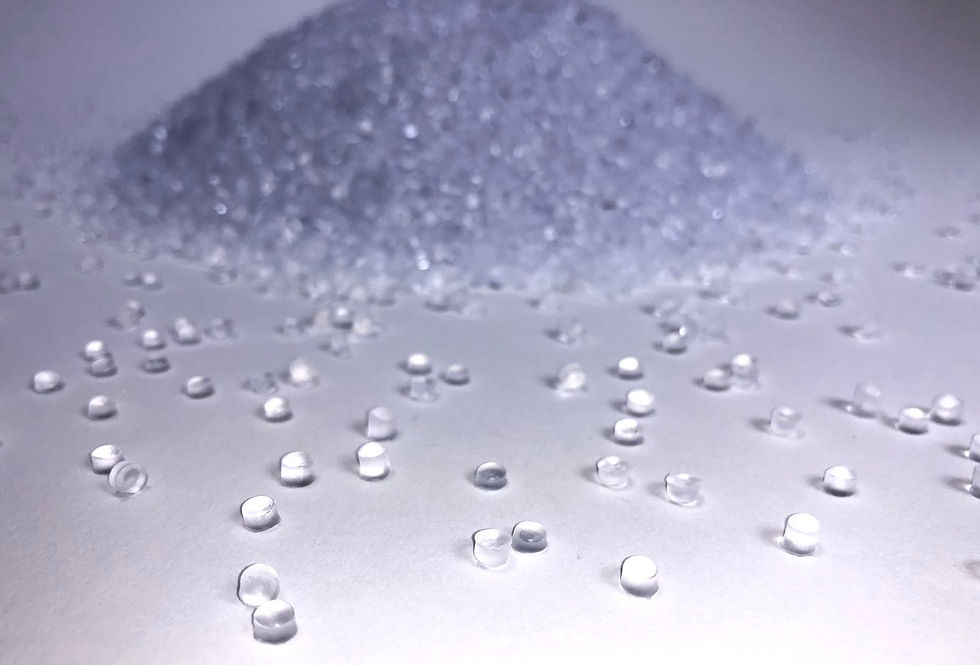
There is much more to buying equipment than the initial price. Whether you are starting out in manufacturing, adding capacity, or replacing older equipment, machinery for the extrusion, molding, blow-molding and vacuum-forming of plastics is a significant investment in the future of your company. The key question, above all others, is the availability of ongoing support, maintenance and spare parts for the equipment that you wish to purchase.
All machines have components that wear down and break and must be replaced in the normal course of converting raw materials into finished goods. Initially, you may think that a low-cost machine from Asia is the key to your success, but unless your supplier can provide you with accurate repair and maintenance manuals, as well as training, ongoing support and spare parts, your business could be at risk. Maintenance events are a matter of when, not if!
Similarly, if you are considering buying used equipment, look into whether accurate repair and maintenance manuals and training, ongoing support and spare parts are available. Equipment made several years, or even decades ago, may not have the control-loop feedback mechanism to maintain temperature and pressure precisely, or the data availability to allow you to make your products accurately and with little scrap. It may not be easy, or even possible, to retrofit older systems with PID controllers for automatically applying corrective responses to shifts in preset operating conditions for a given die or mold. Nor may it be possible to retrofit them with readouts with big, easy-to-read numbers or a system that allows easy referral to stored data.
Other factors that weigh in!
Typical components that need replacing include screws, barrels, seals and bushings. The size and weight of these components is a consideration and defines the infrastructure needed to maintain them. A molding machine weighing 10 tons can be delivered and installed in place by a machinery mover, but what will be involved in removing and replacing a screw which may weigh upwards of 300 pounds, or a barrel which may weigh upwards of 600 pounds? Many machines have components which weigh upwards of 1 ton. To keep your machinery running, you will need to use overhead cranes and/or other lifting equipment. This is both expensive and time-consuming.
Another critical factor is the energy use by the entire production line for every pound of material processed. The cost of energy is a significant factor in converting plastic resin to finished goods. The price of electricity is only going up. Consider how many kilowatt hours are required per pound of material being processed and the impact on your business if energy prices go up by 50% to 100%.
Yet another critical factor is footprint.
Modern equipment using the latest technology will not only consume far less power than older designs, but also occupy much less floor space. If for example, you can purchase a new modern line to convert resin into sheet products which is 10x smaller than equipment based on older technology, the savings are significant and the opportunity to put more equipment in your existing space can allow your business to grow. Furthermore, replacing an old extrusion line with a modern one may allow multiple lines to be installed in the same space, and may use less power than the original line.

The purchase of extrusion and other plastic processing equipment can be very complex. Vendors will tout the merits of a particular screw and barrel design including the dimensions of the screw, channel depths, and materials choices. These are important considerations. But remember, a faster screw rpm doesn’t necessarily mean more output/hour, as higher frictional heat development may make it undesirable.
What really counts is your ongoing cost to produce each unit of usable output. Ask your vendor how many pounds of material you need to run at the start and to purge the machine and stabilize output with the control system provided. Modern machines with preset values for a die and closed-loop temperature, pressure and dimensional controls can provide more time making product and less time making scrap.
Risk Aversion!
The best way to really understand the costs associated with converting raw plastic resin to a finished product is to work with your proposed supplier to have them demonstrate that they can make your product at the cost that you need.
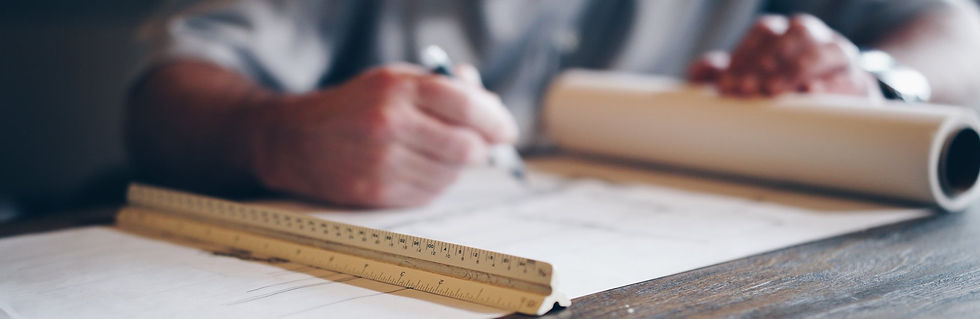
A supplier should be able to take your part drawing, create a die design, and propose a plan whereby you pay a modest amount to have the die made and run on the supplier’s equipment to demonstrate that the equipment can produce the product to the dimensions required and at the production rate promised. By doing this, and tying your final payment for the equipment to performance at the supplier’s facility, you mitigate the risk of having a nasty surprise when you start to manufacture in your own facility.
Importantly, some companies will provide ongoing service for a fee including a technical support line and rapid (1 or 2 day) shipping of spare parts. This can minimize your down time and ensure the longevity of your investment at a predictable cost, while also minimizing the staffing that you need for ongoing maintenance. For example, some modern extrusion machines producing upwards of 1,000 pounds per hour are modular and replacing a barrel, screw, motor/gearbox, or control panel can be accomplished by two people, without cranes or heavy lifting equipment, in one to two hours, not days or weeks.
The bottom line!

It’s hard to go wrong if you follow these steps.
First, determine the part or parts you want to make and have your supplier demonstrate that they can make them on their equipment.
Second, understand the costs of delivery, installation, and training on how to use and maintain the equipment.
Third, ensure that you have ongoing access to a technical support team and to the prompt delivery of spare parts.
Finally, ensure that the equipment is properly insured during transit, loading and unloading, and when being installed.
Comments